Streamlining Lateral Patient Transfers with SimPull from The Patient Company
The Challenge
The Patient Company designed SimPull, a lateral patient transfer device used to transfer patients safely and respectfully between hospital beds. SimPull eliminates the need for staff members to lift or produce force to move patients, instead enabling the staff members to move patients safely.
The Patient Company approached Hatch with pre-production prototypes that they needed to source and manufacture. Hatch’s task was to review and refine the design for mass production, develop the supply chain, reduce the Bill of Materials (BOM) cost, and ultimately began manufacturing units to meet sales demands. This was made all the more delicate as The Patient Company was in the middle of FDA testing for the product.
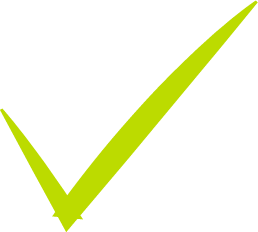
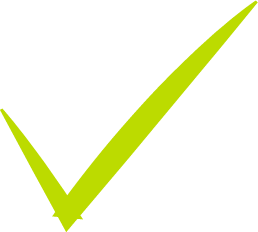
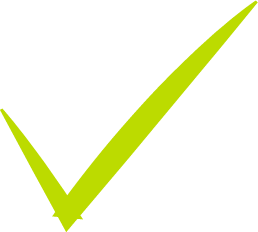
Cost Analysis
Upon receiving the design documents, Hatch conducted a BOM teardown analysis, evaluating vendor pricing, tooling vs. COTS, sourcing options, design, and assembly costs. The analysis identified opportunities to cut costs and improve manufacturing efficiency, aiming to save up to 25% on large orders. After a competitive review, The Patient Company chose Hatch for the project based on its cost analysis and practical Design for Manufacturing approach.
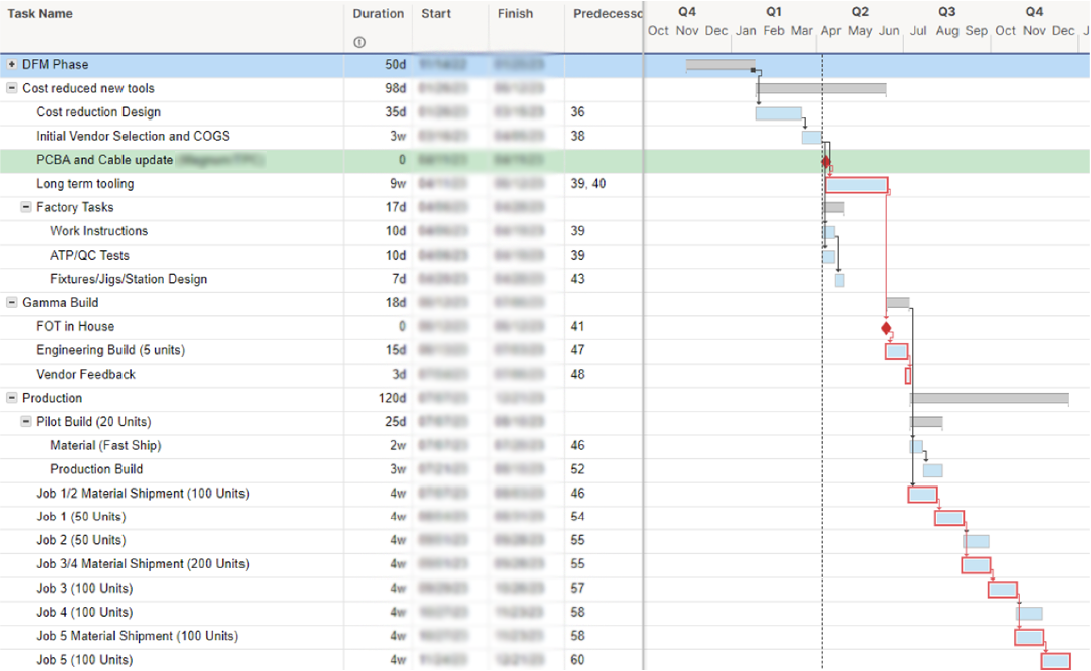
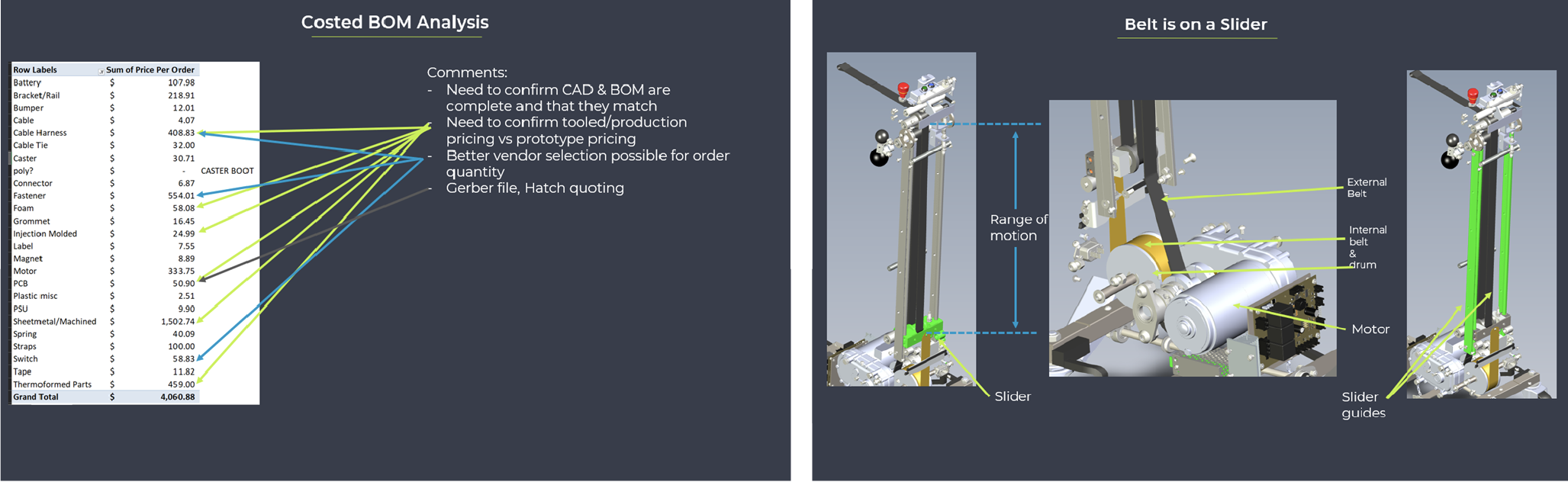
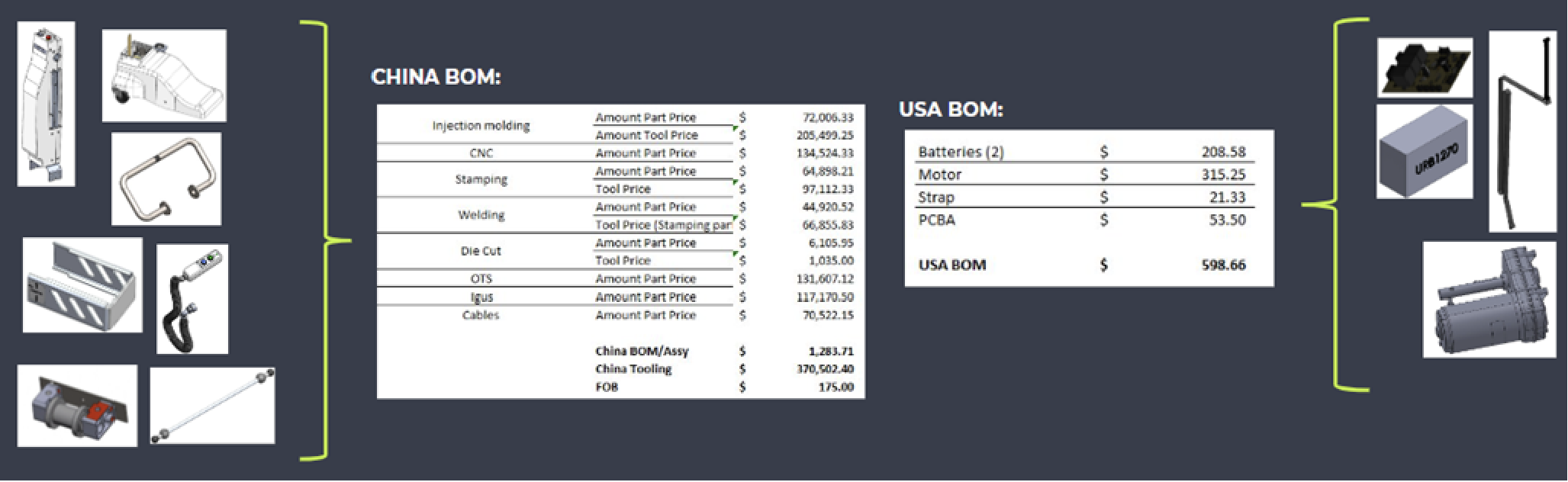
Design for Manufacturing
The Design for Manufacturing phase balanced achieving critical ROIs with ongoing FDA registration testing. Hatch meticulously reviewed over 200 BOM components to optimize material usage, production time, and tooling, which led to significant cost reductions.
Notable improvements included redesigning components for better tooling, which reduced costs and enhanced production quality and efficiency. The Hatch team also took a holistic approach to supply chain optimization, developing a strategic international sourcing and logistics plan.
The redesign resulted in a comprehensive 200+ page document detailing all changes and achieved a 25% reduction in BOM costs during the low-volume pilot build.
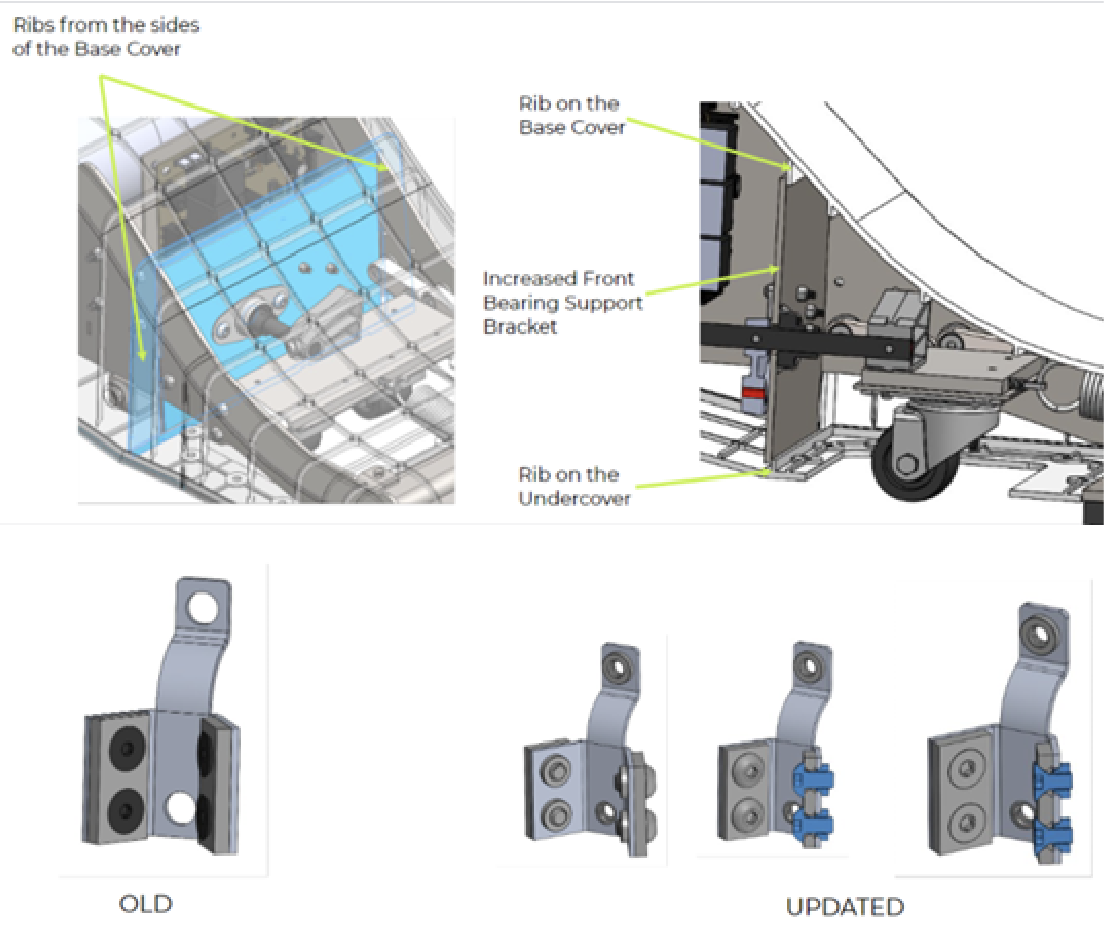
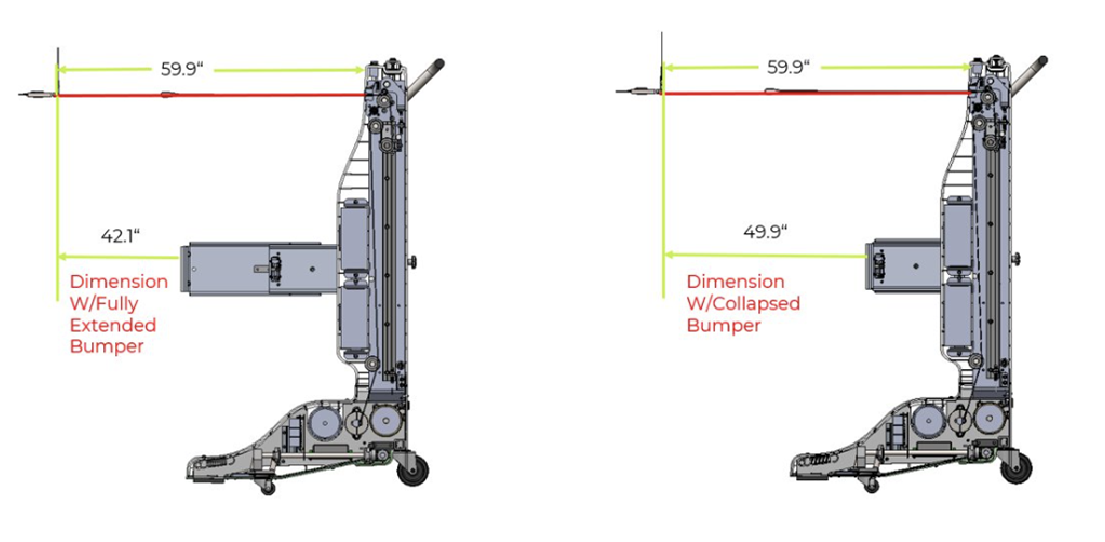
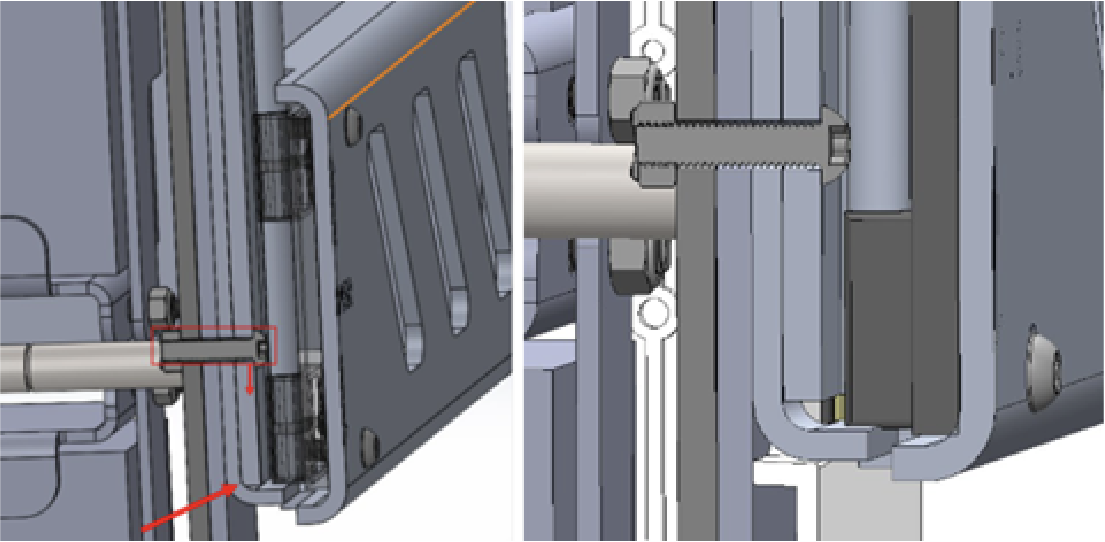
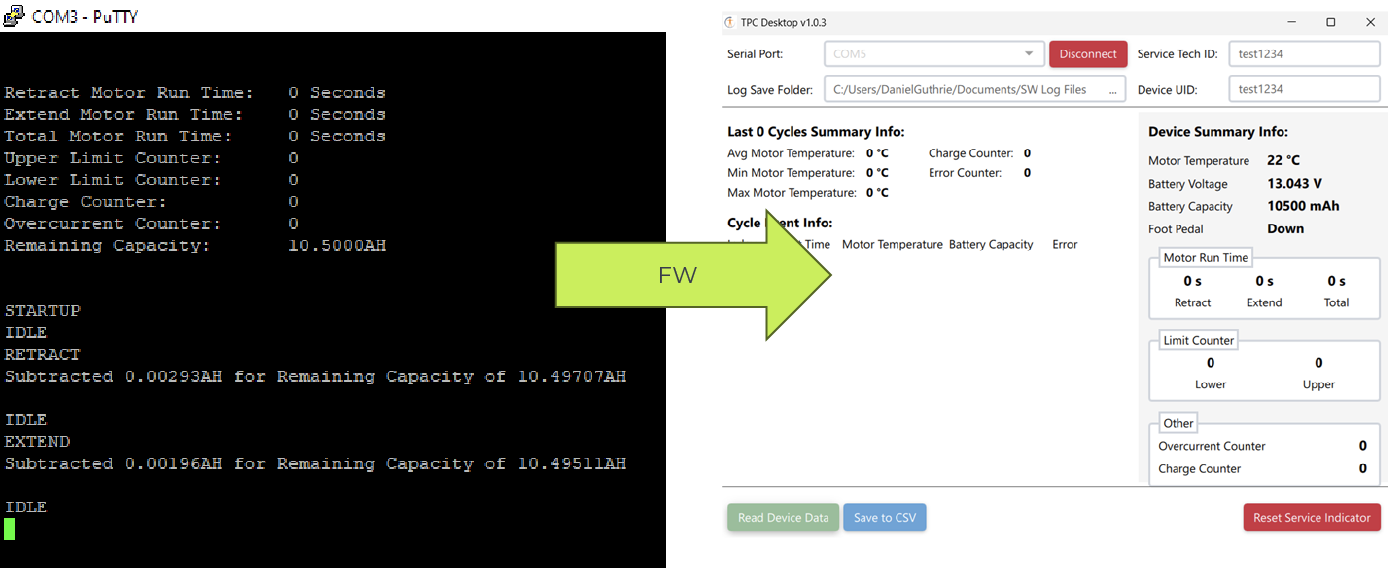
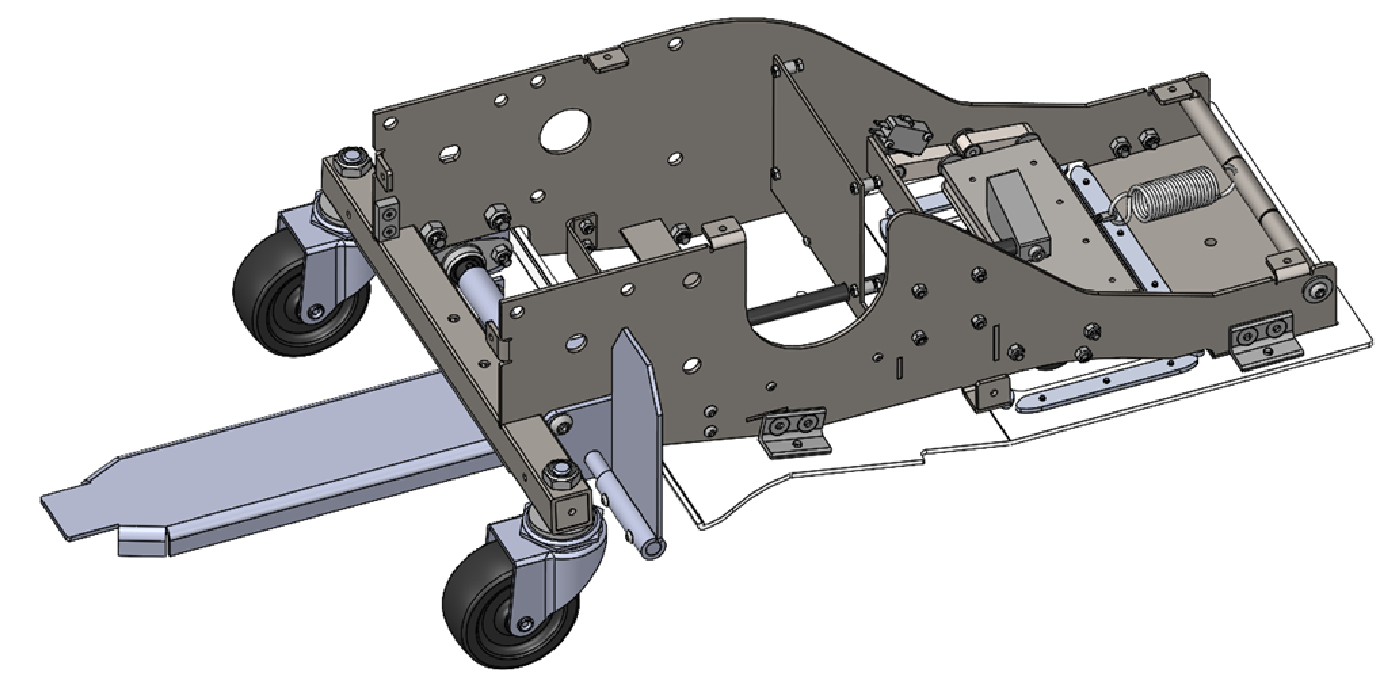
Adding Functionality
Ahead of schedule, The Patient Company requested three additional features. First, the device’s bumper was redesigned to extend and lock for better compatibility with diagnostic beds. Second, the braking lever was converted to a foot pedal for easier use by hospital staff. Third, the firmware was enhanced to include monitoring logs, and a PC App was developed for improved serviceability while maintaining FDA compliance.
The added functions allow SimPull to provide multi-function patient movements. The device can be leveraged for lateral patient transfer, supine to sitting adjustments, patient boosting, and precise positioning for imaging procedures. These updates also enable future upgrades, including accessory mounting and cloud-based dashboard integration. Hatch kept the production BOM within the initial cost goals throughout this process.
Gamma Build of Prototypes
The Gamma Build of SimPull tested the new tools and supply chain, allowing for final debugging and adjustments to near-production parts, minimizing errors and delays.
Units made with final tools provided a near-final product representation. Hatch then conducted Design Verification Testing (DVT) to assess performance against specifications and ensure durability.
Simultaneously, Hatch performed a First Article Inspection (FAI) to verify that initial production parts met design requirements, ensuring quality and consistent production capability.
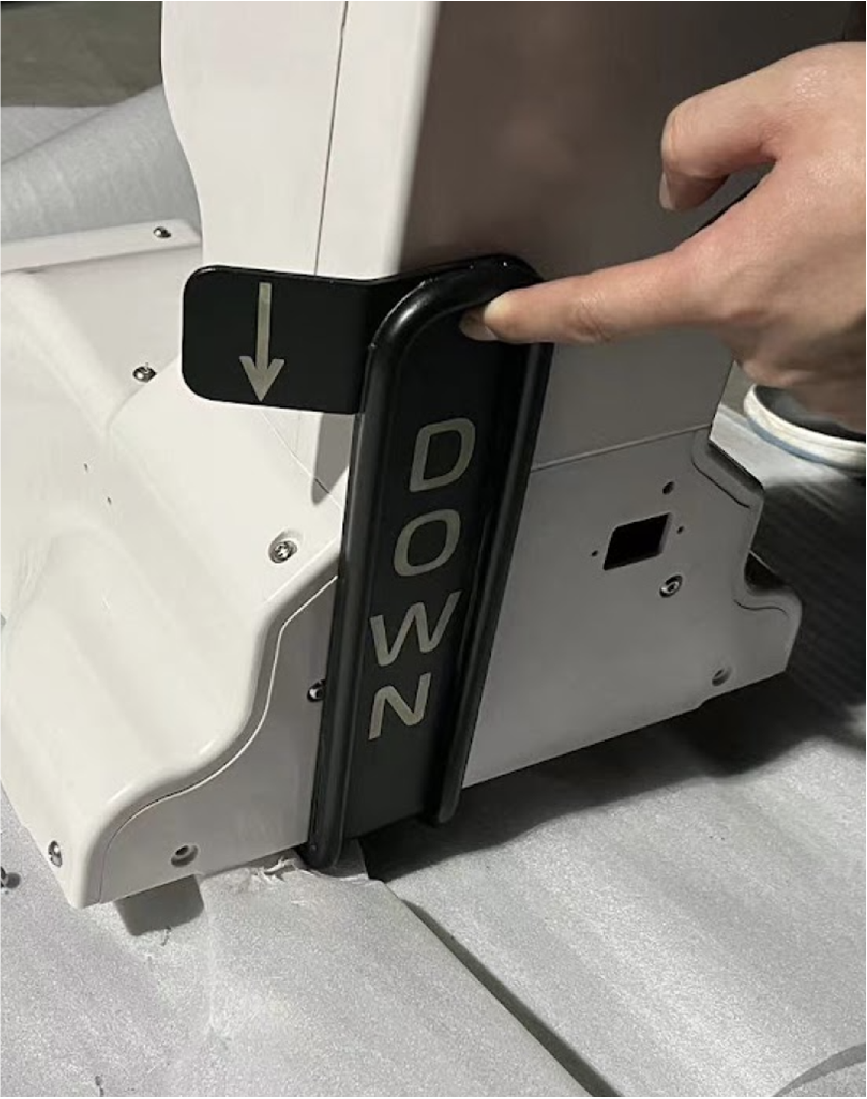
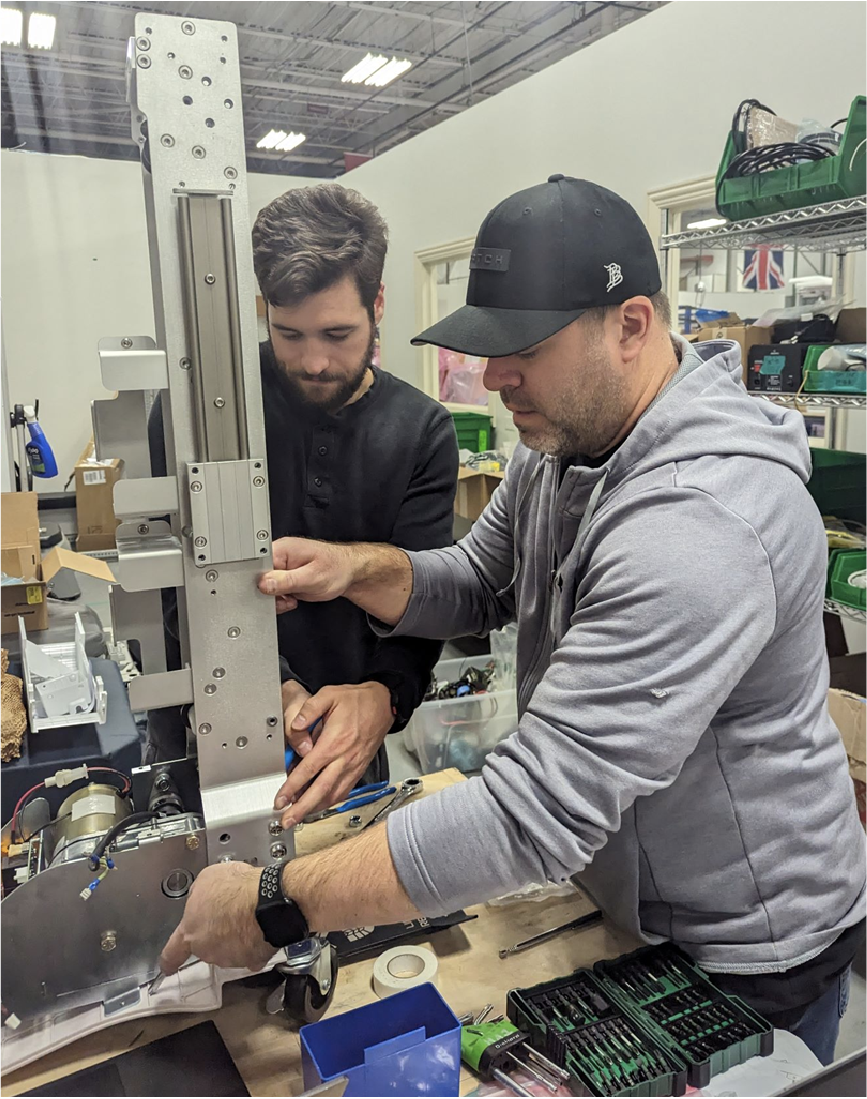
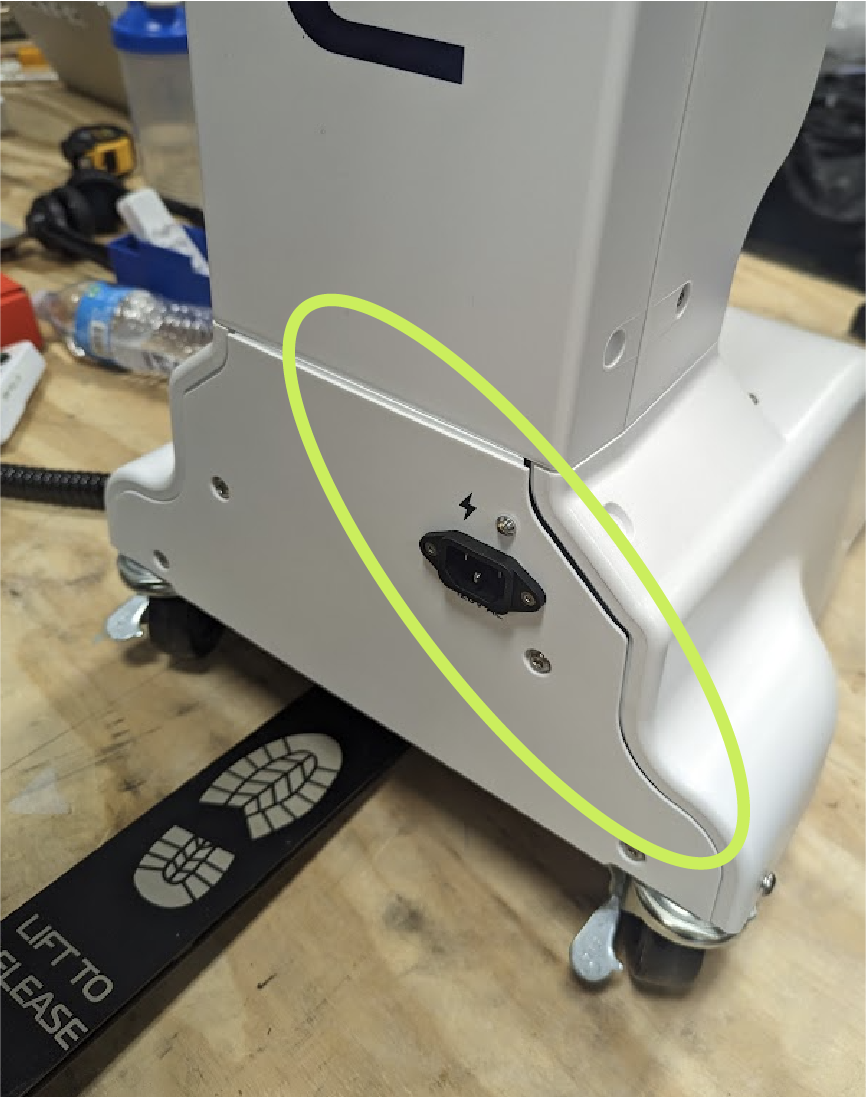
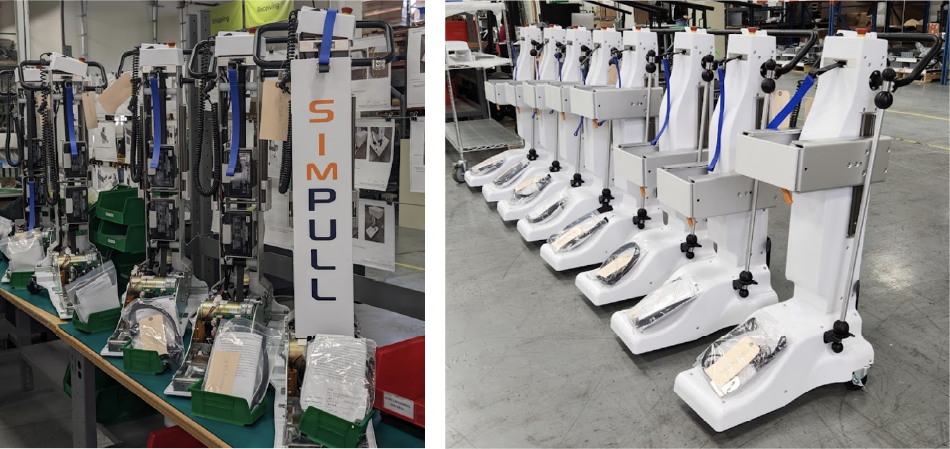
Production Ramp Up
The Gamma Build verifies the Assembly Work Instructions and Acceptance Test Procedures.
Assembly Work Instructions detail the steps, tools, materials, and quality checks for error-free production, while Acceptance Test Procedures outline tests and inspections to ensure product specifications are met.
Both documents are reviewed and approved by Hatch engineers and specialists before use. They also guide assembly line setup, optimized for workflow and equipment, and are verified through a production time study reviewed by Hatch and The Patient Company teams.
Contract Manufacturing & Quality Control
After the Gamma Build, Hatch released the manufacturing documents for The Patient Company’s first Engineering Change Notice (ECN) in March 2024.
The initial 100 units were split into a 10-unit batch for early issue detection and a 90-unit batch for cost-effective sea shipping of subassemblies. Final device assembly is then completed at Hatch’s US manufacturing facility. This approach reduced waste and ensured a smooth transition to full-scale production.
The pilot build also supports Hatch’s ISO13485 certification efforts, crucial for ensuring quality in medical device manufacturing.
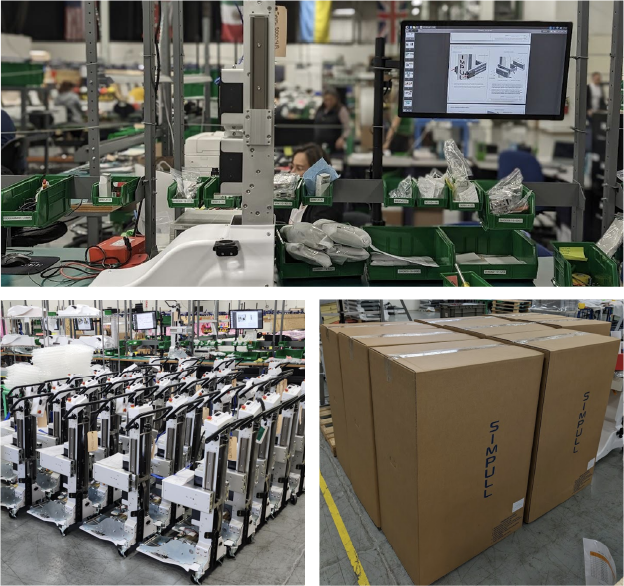