In the fast-paced world of product development, bridging the gap between off-the-shelf evaluation kits (EVKs) and fully customized Printed Circuit Board Assembly (PCBA) prototypes is critical. At Hatch, we specialize in product development and contract manufacturing, offering robust prototyping capabilities that empower businesses to evolve their ideas from evaluation kits into complete, functional hardware.
This blog will guide you through the process of transitioning from an EVK to a fully customized PCB prototype board assembly, focusing on both the firmware development process and the prototyping expertise we bring to the table. We'll also explore the importance of testing, fixturing, and automated board checks in ensuring quality and efficiency.
1. Leveraging EVKs for Firmware Development
Evaluation kits are an essential tool during the early stages of product development. These kits provide pre-configured hardware and software platforms that allow developers to quickly test and validate firmware and software features before committing to a custom hardware solution. EVKs accelerate the initial development process, helping to refine algorithms, user interfaces, and functionalities in a controlled environment.
However, while EVKs offer a flexible starting point, they often come with limitations in terms of scalability and hardware customization. As your product grows in complexity or moves towards market readiness, you’ll eventually need to move beyond the EVK and design a custom PCB assembly that’s tailored to your specific application requirements.
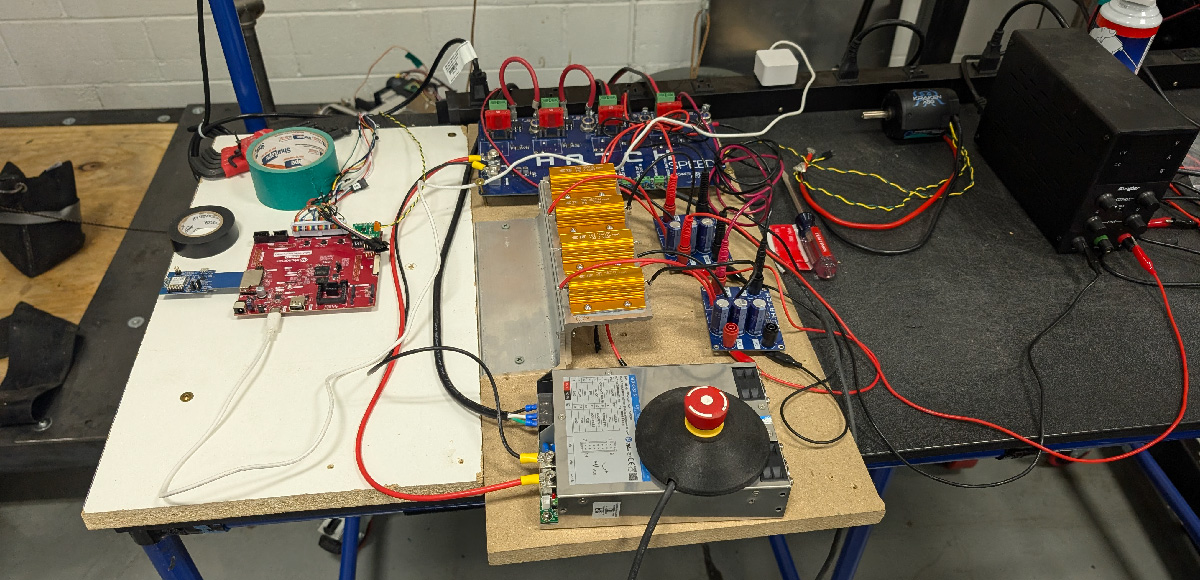
2. Ensuring Feature Completeness in Software
As you develop your software on an EVK, it’s important to ensure that all critical features are thoroughly tested and validated. EVKs allow for a controlled environment where you can experiment with different configurations, sensors, and modules to confirm functionality. Hatch’s experience in software development allows us to optimize this process, ensuring that the software is robust and feature-complete before transitioning to custom hardware.
During this phase, it's crucial to focus on compatibility, performance, and integration with the hardware you intend to build. Making the software modular and adaptable will ease the transition to a custom PCB assembly later on.
3. Designing Your Custom PCB Prototype Board Assembly
Once you’re confident that the software meets your needs, it’s time to transition from the evaluation kit to a custom PCB prototype assembly. This step is where Hatch’s advanced prototyping and manufacturing capabilities shine. Our team works closely with you to design a PCB assembly that meets your exact specifications—whether it’s miniaturization, power efficiency, or additional functionalities.
Custom PCB assembly prototyping at Hatch is a collaborative process, which includes:
- Schematic and Layout Design: We translate your EVK-based designs into custom schematics and PCB layouts that are tailored to your product's requirements.
- Component Selection: Based on the needs of your software and desired features, we help you select the most appropriate components.
- PCB Assembly Fabrication: Working with vendors who use cutting-edge manufacturing processes, we can prototype your custom PCB assembly, ensuring the highest level of precision and quality.
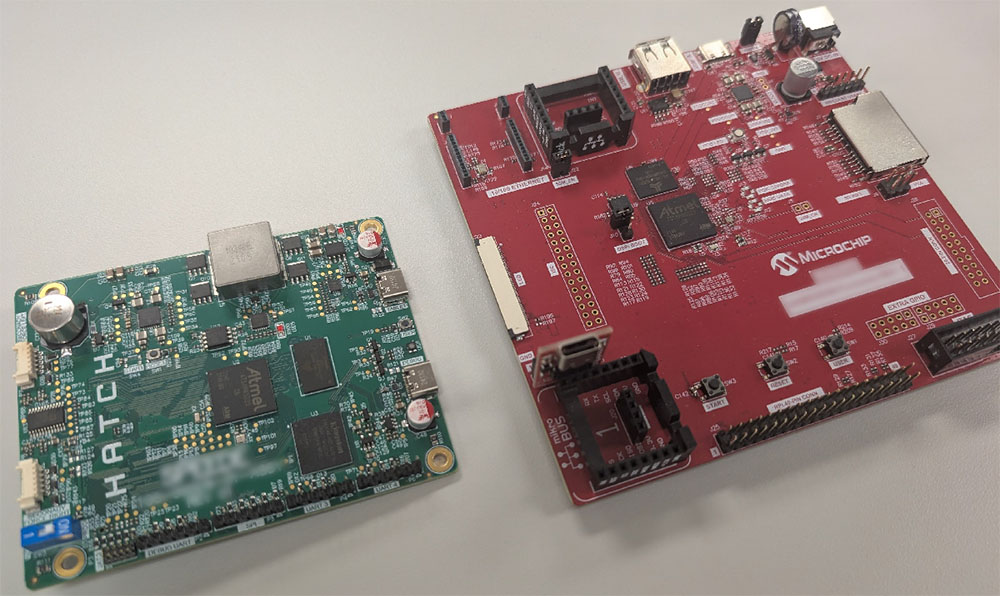
4. Testing: The Key to a Reliable PCB Prototype Assemblies
The transition from an EVK to a custom PCBA prototype isn’t just about assembling components—rigorous testing is crucial to ensure the design’s functionality and reliability. At Hatch, we offer a range of testing capabilities that streamline the validation of your custom PCB Assemblies.
- Test Fixturing: We develop custom test fixtures that simulate features and validate the electrical performance of your prototype. Test fixtures allow us to quickly identify and resolve issues related to signal integrity, power distribution, and component interaction.
- Automated Testing: Our testing facilities enable us to perform automated checks of your PCB assemblies. This includes continuity testing, signal analysis, and performance benchmarking, all of which help to ensure the board meets your design specifications.
By combining manual and automated testing processes, we ensure that your PCB prototype assemblies function as intended in various conditions. This reduces the likelihood of issues later in production and in the field, saving time and resources in the long run.
5. Integrating Firmware with Custom Hardware
As the custom PCB assembly moves through the prototyping phase, the next challenge is ensuring seamless software integration. Since the firmware has been developed on an EVK, there may be slight adjustments needed to accommodate the differences between the EVK’s hardware and the custom PCB assembly. Hatch’s engineering team supports this transition by:
- Adapting the firmware for the new board configuration.
- Ensuring compatibility with any new sensors, inputs, or interfaces added to the custom PCB assembly.
- Conducting thorough tests to confirm that all features function correctly in the final hardware environment.
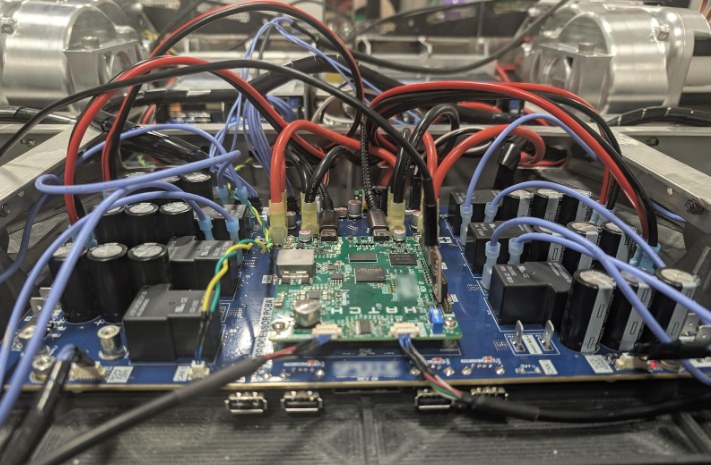
6. Scaling from Prototype to Production
Once your custom PCB prototype assembly has been fully validated, the next step is scaling for production. Hatch’s contract manufacturing services are equipped to handle this process seamlessly. From low volume manufacturing to mass production, we optimize every step for efficiency and quality. Our integrated approach ensures that the final product maintains the high standards established during the prototyping phase.
The journey from an evaluation kit to a fully customized PCBA prototype board involves careful planning, collaboration, and rigorous testing. At Hatch, we bring decades of experience in product development, prototyping, and contract manufacturing to ensure a smooth transition. Our software and hardware expertise, combined with our manufacturing capabilities, make us the ideal partner for transforming your EVK-based concepts into fully realized, market-ready products.
Let Hatch guide you through the prototyping process and beyond—get in touch with our team today to learn how we can help bring your ideas to life.